Zinc Alloy Die Casting
High pressure die casting - particularly of zinc alloy - is the quickest route from molten metal to finished product, especially in mass production. Zinc diecasting products are widely used in many everyday applications, from zippers, buckles , toy cars and furniture components to automobile, electrical and mechanical hardware. Thanks to its good flexibility on the choice of surface treatment, zinc diecasting components are widely used in decorative applications as well.
- Flexibility and responsiveness to meet your specific needs
- Increase your profitability & lowering production costs
- High-quality production of unique or custom products
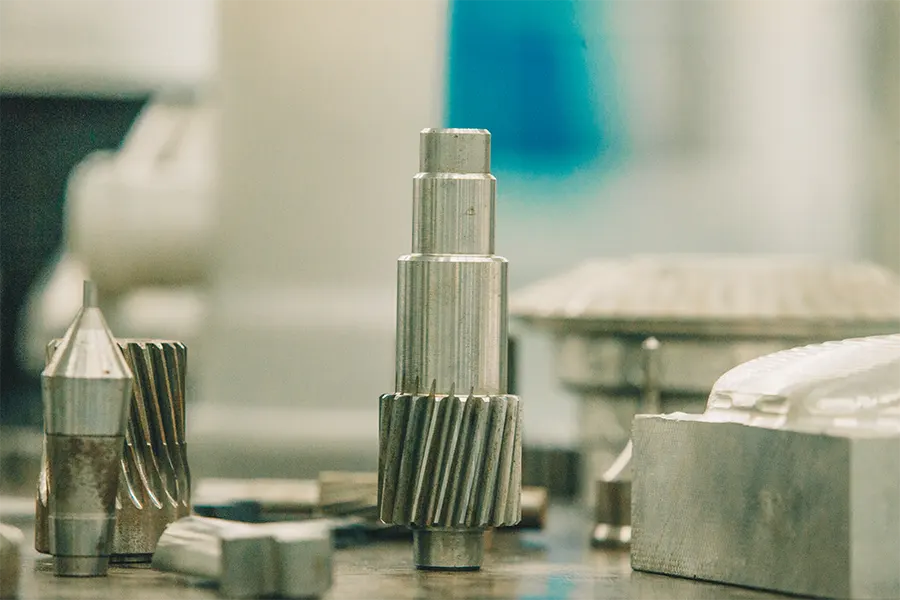
- Overview
- Feature
- Materials
- Finishes
- Why Choose Us
- Resources
Zinc Alloy Die Casting Solutions
From Prototyping to Production
Zinc alloy die casting offers high strength, precision, excellent surface finish, good conductivity, and cost efficiency. It supports large-scale production, is highly recyclable, and is widely used in automotive, electronics, and other industries, ensuring durability and versatility.
Fast Small Part Molding
Our comprehensive CNC machining service will guide your project from prototype development to final parts production.
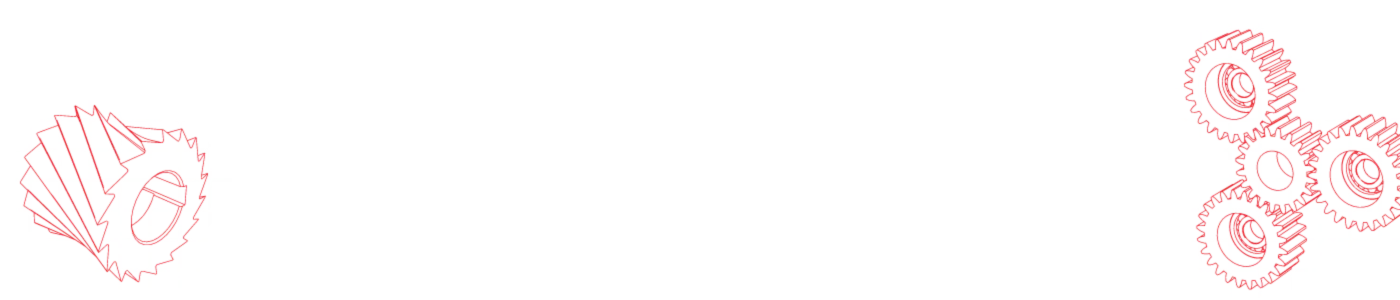
Zinc Alloy Die Casting Materials
Vacuum casting uses silicone molds to produce high-quality parts from a master model, typically made through 3D printing or CNC machining. It’s ideal for functional prototypes, small batches, and complex parts, offering excellent detail and durability.
We can source any other materials upon request! If you don’t see the material you need please contact us
Why Choose Us?
We are driven by our customers' needs, striving to exceed their expectations with outstanding performance. By aligning with shared goals and interests, we deliver exceptional services that enhance our customers' market position while fostering mutual growth and a beneficial partnership.
- Can make up for the risk of large capital investment before mass production.
- Diversified production materials and styles.
- Customers can grasp the production details at any time, and understand the production progress at any time.
- Some other features can be added to the parts in production, which are not restricted by the mold.
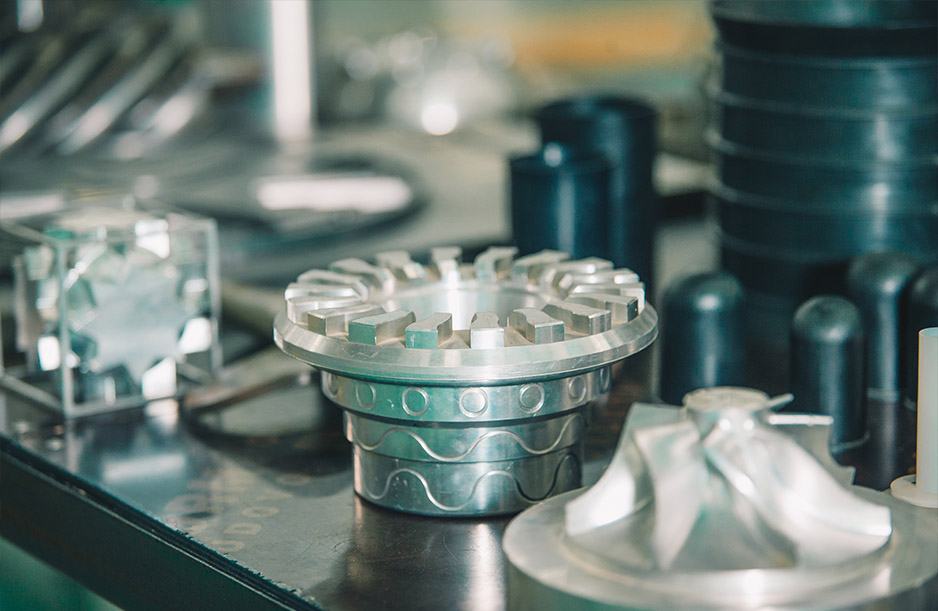
Industry Application
We manufacture millions of parts for a variety of applications, providing best-in-class products for different industries: optics, medical, semiconductor, communications, etc.
FAQs
What materials are CNC machining used for?
What are the advantages of CNC machining?
What are the application areas of CNC machining?
How long does it take to receive a part after an order is placed?
Manufacturing Resources
Start production of your parts today
